Working with a British Tailoring and Family-Owned Mill
he material choice is one of the most important decisions for our product development team at Studio 104. Drawing on years of experience and knowledge, we work in partnership with our suppliers to select the right quality and fabric for each element of our luxury uniform collections. This often includes designing and developing tailor-made fabrics for our clients, therefore we are constantly learning and expanding our team’s knowledge about the weaving process.
On a recent visit to our British tailoring supplier, a traditional family owned weaving mill in the heart of West Yorkshire. We explored the different elements of the weaving process, from the yarns to the finishing.
There are very few vertical mills left in the U.K., the majority like ours buys the yarn pre spun and dyed. This helps with production lead-times to hold stock of key colours ready for orders. The first stage is to create the warp, the warp is a continuous yarn the length of the fabric, which is spun on to a bar for weaving. The design is built into the fabric at this point. The one bwill be become a tartan; you can see how the pattern will grow when the weft is introduced.
This mill has 20 looms, each one running constantly 24/7 to keep up with the demand. To be the most economical with the looms each one is set up to create a certain type of the fabric, some make 100% wool others produce a wool polyester blend. This means that when one batch of fabric is complete the next pattern is tied on, to keep this mill running smoothly.
The fabric is inspected before being sent to the finishers, treads can jump a stitch, or the weaving can pick up contamination of fluff from the air. A department of skilled menders, who have trained for over 2 years, check and repair the fabric, ready to be finished.
Once returned from the finishers the fabric is checked and tested by the mill, and then ready to the be shipped around the world. Our fabrics from this mill are now in front of house uniform’s in Hong Kong for Fortnum and Mason’s, a beautiful deep green twill, and in Scotland for Gleneagles for a bespoke navy tartan to produce exclusively kilts.
As a company striving to be sustainable in our business practices, we aim to work with suppliers who are committed to reducing their environmental impact. Our British tailoring supplier is doing just that. Producing high quality fabrics that will stand the test of time whilst working towards good environmental practices as well as operating in a sustainable manner beyond legal and regulatory requirements.
Solar panels on the mill roof provide 25% of their electricity, with an aim to double that in the next few years. They also have a zero-textile waste policy. All the scraps and off cuts are put to use in the craft industry and the wool fibres as mattress fillings or as recycled textiles. Also, as it is a British supplier, we can always visit and ensure the working conditions are inline with Studio 104 policies.
It is important to all of us at Studio 104 to support UK manufacturing, and it adds something special to our bespoke uniforms to be able to tell clients where our fabrics have come from, down to who was working on the loom.
Written by Bethan @ Studio 104
You might Also Like
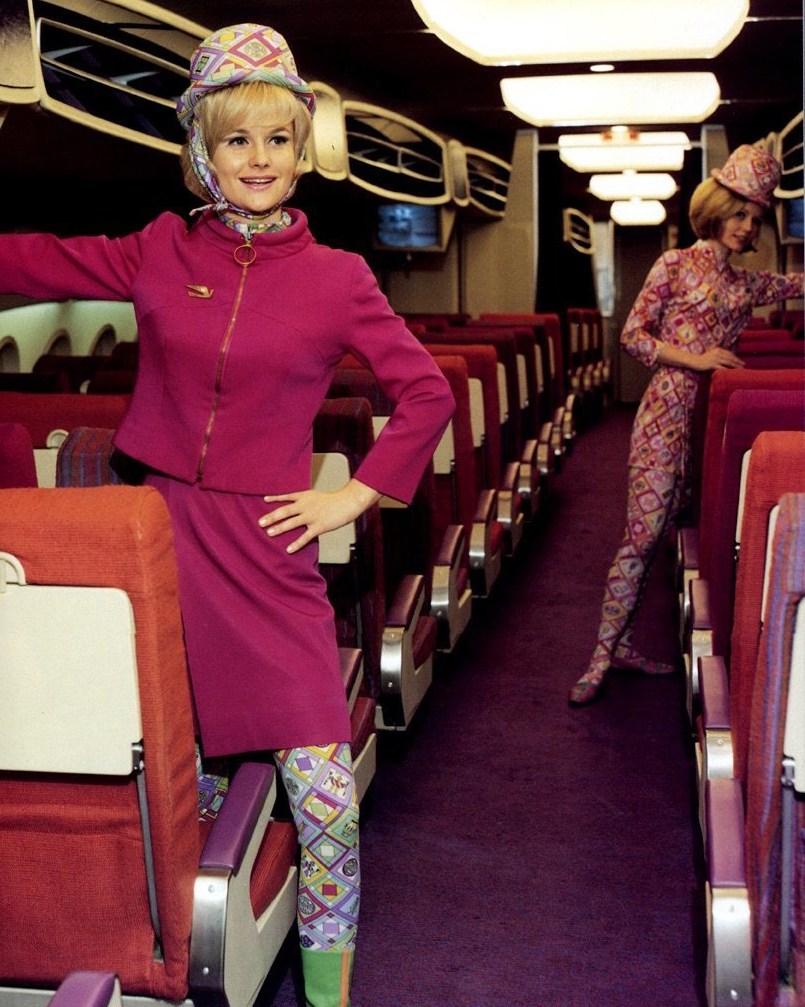
Style at 30,000 Feet - A Trip Through the Evolution of Flight Attendant Style
Could you ever imagine a flight without the reassuring presence of flight attendants there to help us? While flight attendants are constantly on the move, the importance of what they wear doesn’t seem to be going anywhere....
Read More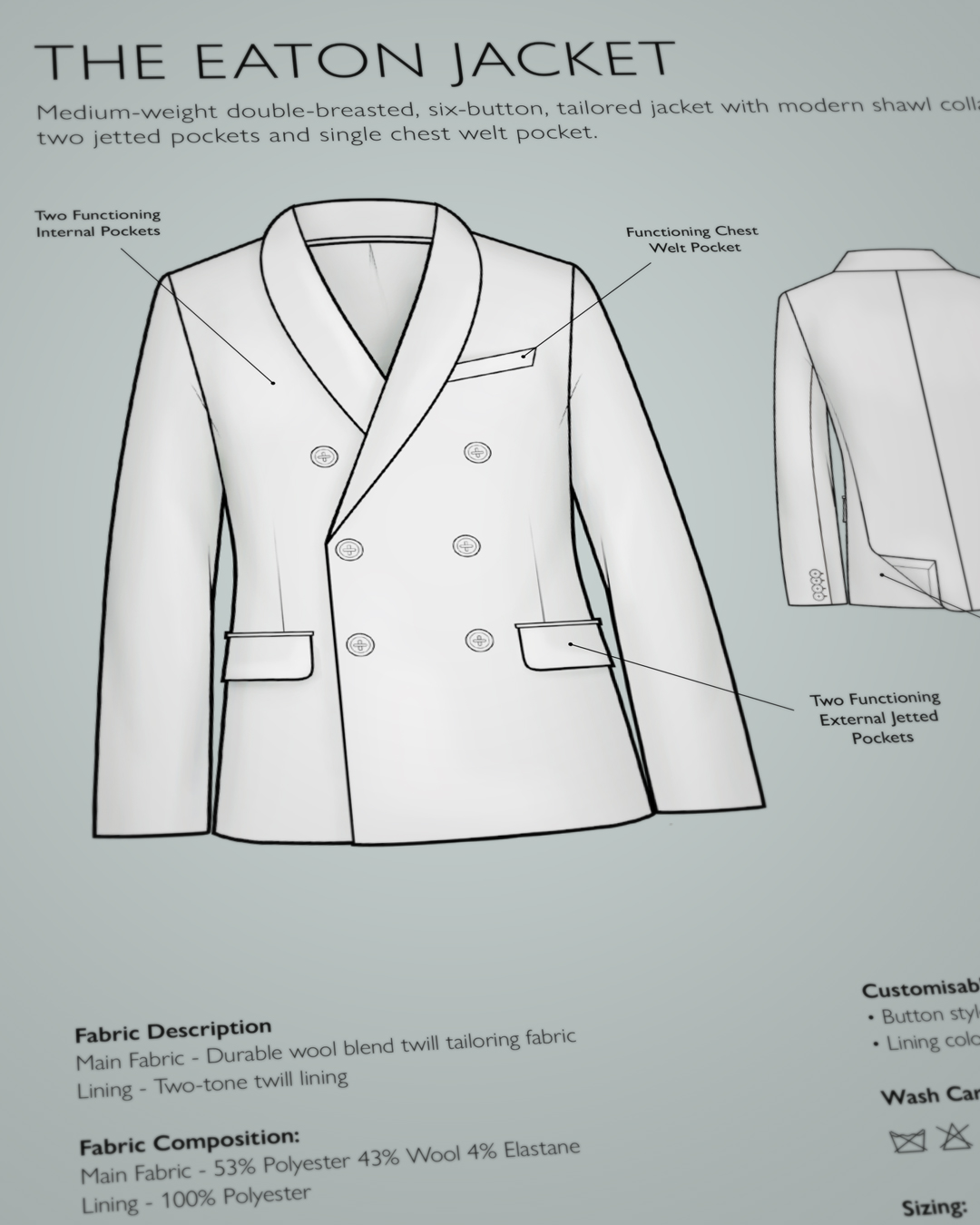
Launch of The 104 Collection - Range Catalogue
Used alongside our look book, this product catalogue aims to help clients easily select key styles and details.
Read More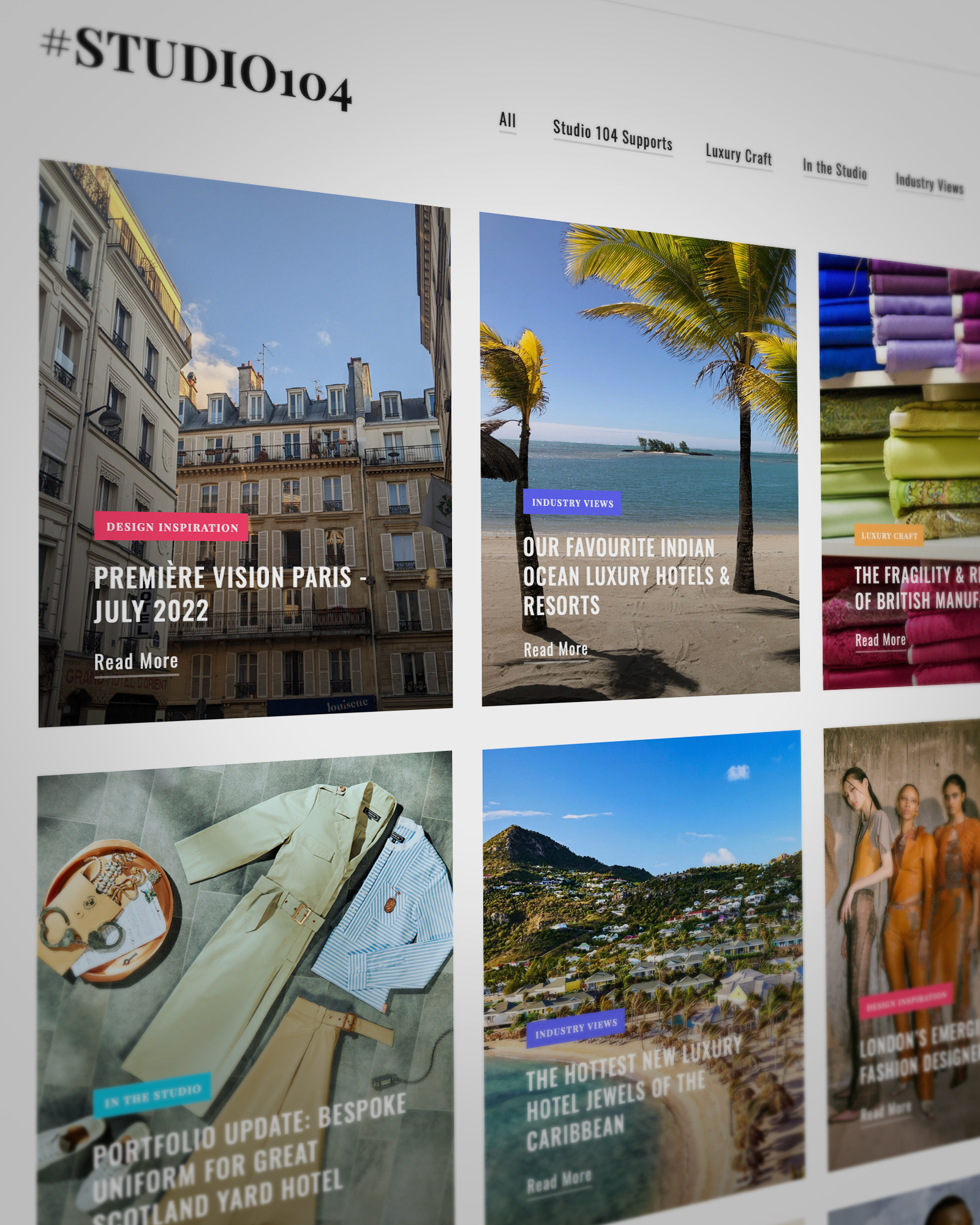
Studio 104 Reaches Blog Number 104
This post is the 104th in the history of Studio 104 blogs. It is a milestone worth noting and a showpiece to the world, displaying what Studio 104 has been in the past, and what it still stands for today - a dedicated high-end service, creating the finest bespoke uniforms for luxury brands worldwide.
Read More